At the Harbor-UCLA Medical Center eye clinic, patients were going blind waiting for treatment. “Sometimes when you work in chaos, you don’t know how to get out of it,” says H-UCLA Chief Improvement Officer Susan Black. The system had to change, and a partnership with Toyota showed them the way. Through a series of small changes, the clinic dramatically cut wait times and completely eliminated a hundreds-long surgical backlog.
Over the past 67 years, Toyota has perfected its Toyota Production System, an integrated social-technical methodology in which small, continuous improvements drive high quality of work and competitiveness. And now Toyota is helping organizations across the US apply its practices to find their own solutions.
Toyota partnered with filmmakers to create a series of short films to document some of the most impactful projects Toyota has embarked on in recent years. Called The Toyota Effect, the series highlights the company’s mission to share their own Toyota Production System for the betterment of people’s lives and organizations through mini-documentary style films.
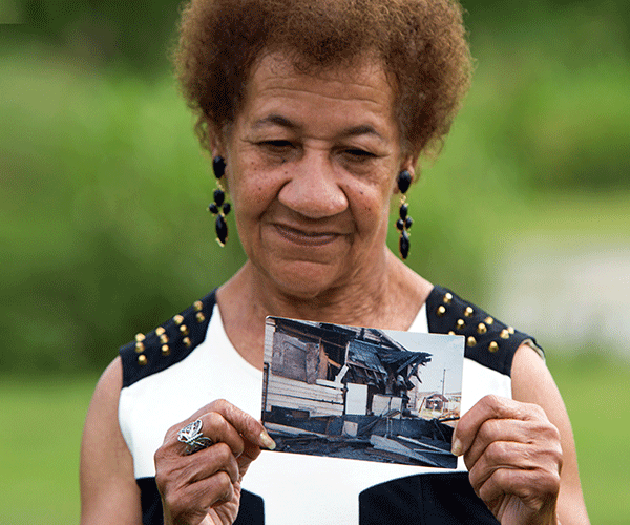
The St. Bernard Project (SBP) had been so successful building homes for families displaced by Hurricane Katrina, its founders expanded to help more communities in need. However, expansion left SBP completing fewer houses. With Toyota’s help, SBP went lower tech, like tracking projects on a whiteboard instead of a computer—and almost doubled the number of homes they built in a year. CEO & Co-Founder Zack Rosenburg: “You can hide things in a computer. You can’t hide things in a whiteboard. The whiteboard system makes sure that you have a clear schedule—with daily goals—and that, every day, for every task, for every house, you know if you are ahead or behind.”
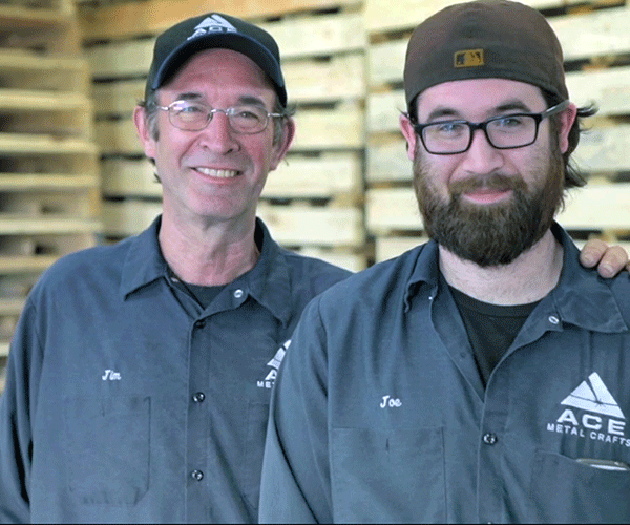
The employees of ACE Metal Crafts, one of the country’s only domestic manufacturing firms, were hesitant to let an international company tell them what to do. But ACE couldn’t finish projects on time, and its leadership needed help figuring out why—so they turned to Toyota. The result: ACE not only revamped its entire process and increased business, it hired 20 more people. CEO Jean Pitzo says of the experience, “We see a bright future with an abundance of growth opportunities that will help us with our purpose to unleash potential in people.”
As these organizations discovered: No matter how good your intentions or outcomes—if your process is dysfunctional, you’ll never accomplish all the good you could. And when good ideas are shared, everyone wins.
Check out The Toyota Effect’s documentary-style series of mini-films here.